Not known Facts About Alcast Company
Table of ContentsExcitement About Alcast CompanyAbout Alcast CompanyThe smart Trick of Alcast Company That Nobody is DiscussingExamine This Report about Alcast CompanyThe Best Guide To Alcast CompanyGetting The Alcast Company To Work
The subtle distinction depends on the chemical web content. Chemical Comparison of Cast Light weight aluminum Alloys Silicon promotes castability by lowering the alloy's melting temperature and boosting fluidity throughout casting. It plays a critical function in permitting detailed molds to be loaded accurately. Additionally, silicon adds to the alloy's stamina and put on resistance, making it valuable in applications where longevity is critical, such as automotive components and engine components.It also enhances the machinability of the alloy, making it easier to process right into ended up items. This way, iron contributes to the overall workability of aluminum alloys. Copper raises electric conductivity, making it beneficial in electrical applications. It additionally boosts rust resistance and contributes to the alloy's general stamina.
Manganese adds to the toughness of aluminum alloys and enhances workability. Magnesium is a light-weight component that supplies strength and influence resistance to aluminum alloys.
The 8-Minute Rule for Alcast Company
It permits the manufacturing of lightweight elements with excellent mechanical properties. Zinc improves the castability of light weight aluminum alloys and assists manage the solidification procedure during casting. It improves the alloy's toughness and hardness. It is typically found in applications where detailed forms and great information are required, such as ornamental castings and particular vehicle components.

The primary thermal conductivity, tensile strength, yield stamina, and elongation vary. Amongst the above alloys, A356 has the highest possible thermal conductivity, and A380 and ADC12 have the lowest.
A Biased View of Alcast Company
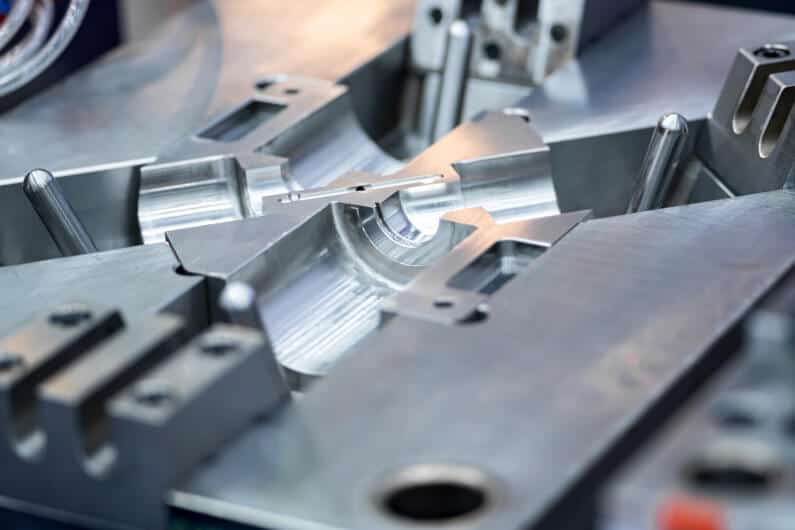
In accuracy spreading, 6063 is well-suited for applications where elaborate geometries and top quality surface area coatings are vital. Instances consist of telecommunication enclosures, where the alloy's remarkable formability permits for smooth and aesthetically pleasing styles while maintaining architectural stability. In the Lighting Solutions sector, precision-cast 6063 elements develop stylish and reliable lights components that call for detailed shapes and great thermal performance.
It causes a better surface finish and much better corrosion resistance in A360. The A360 exhibits remarkable elongation, making it perfect for complex and thin-walled parts. In precision spreading applications, A360 is well-suited for industries such as Customer Electronics, Telecommunication, and Power Devices. Its improved fluidity permits elaborate, high-precision elements like mobile phone housings and interaction gadget real estates.
5 Easy Facts About Alcast Company Explained
Its special properties make A360 an important option for accuracy spreading in these sectors, enhancing product toughness and top quality. Casting Foundry. Aluminum alloy 380, or A380, is a widely used casting alloy with several distinctive qualities.
In precision spreading, aluminum 413 beams in the Customer Electronics and Power Devices markets. This alloy's exceptional corrosion resistance makes it a superb option for outdoor applications, making certain resilient, durable items in the discussed industries.
The 6-Second Trick For Alcast Company
As soon as you have determined that the aluminum die casting procedure appropriates for your job, an important following action is making a decision on one of the most suitable alloy. The light weight aluminum alloy you pick will substantially affect both the spreading process and the properties of the final product. Due to the fact that of this, you should make your decision meticulously and take an informed approach.
Identifying the most suitable aluminum alloy more for your application will certainly indicate evaluating a broad range of characteristics. The first group addresses alloy features that impact the manufacturing process.
The Best Guide To Alcast Company
The alloy you pick for die spreading directly affects a number of aspects of the spreading procedure, like exactly how easy the alloy is to deal with and if it is prone to casting flaws. Hot cracking, likewise known as solidification fracturing, is a common die spreading problem for light weight aluminum alloys that can lead to internal or surface-level rips or cracks.
Certain aluminum alloys are extra prone to hot cracking than others, and your option ought to consider this. It can damage both the cast and the die, so you must look for alloys with high anti-soldering buildings.
Deterioration resistance, which is already a notable quality of light weight aluminum, can differ considerably from alloy to alloy and is a necessary particular to take into consideration depending on the environmental conditions your product will be exposed to (Foundry). Use resistance is one more building generally looked for in light weight aluminum items and can set apart some alloys